Manufacturing Processes
Tianjiang owns a total of 30 patents for full spectrum herbal extract invention and all the independent intellectual property rights of key technologies for granule herb production. Tianjiang's patented extraction methods utilize a new generation of technology, producing granules that dissolve better and come out like a decoction.
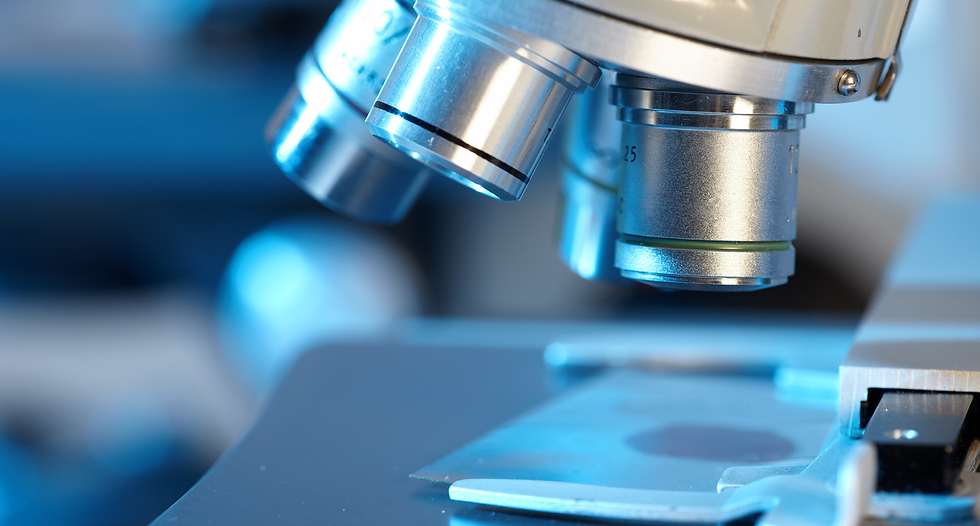
1. Raw Herb Authentication Tests

2. Traditional Processing /PaoZhi
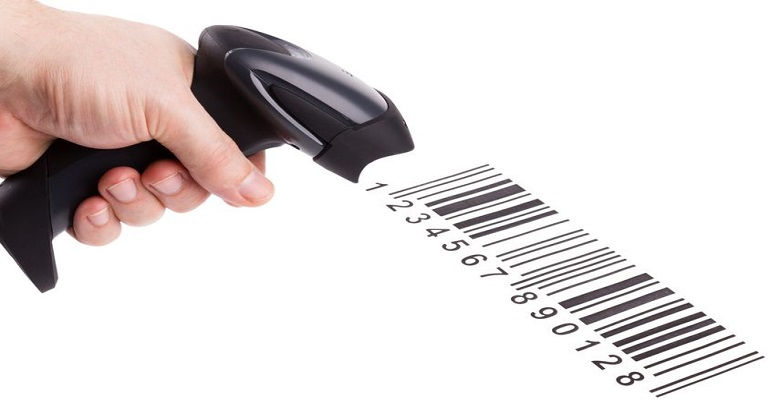
11. Safety Tracking
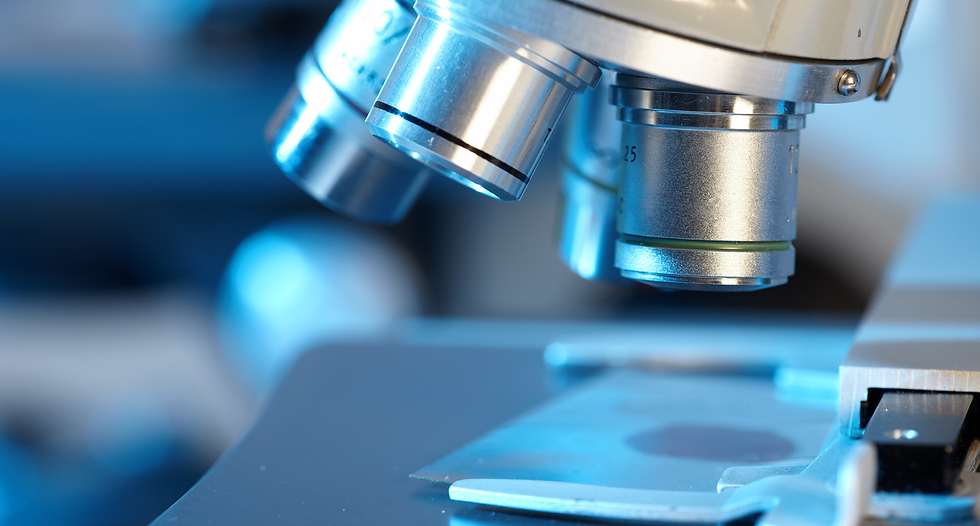
1. Raw Herb Authentication Tests
Traditional Raw Herb Processing / Pao Zhi
Once the authentic raw herbs are selected, they are cleaned and prepared according to the traditional Pao Zhi method to reduce the toxicity and side effects that some herbs have, while promoting their therapeutic effects. All traditional Chinese medicine processing methods and “Chinese Pharmacopeia” standard requirements have been adopted to enhance the quality of the products. Our methods for processing raw herbs include stir-frying with liquid adjuvants, steaming, parching, germinating, fermenting, and freezing.
Our full spectrum herbal extracts are extracted with purified water and are stewed individually, in adherence with traditional methods of decoction, in order to maximize the medicinal value of each herb. A fully automated system of new generation extraction machines allows the decoction process to be customized for raw herbs in a variety of forms including rhizomes, flowers, fruits, entire plants, and seeds, which are then classified into the following categories: sugar-containing, natural base, glycoside, fat-soluble, water-soluble, and essential oil. During water-based extraction, the essential oils are collected to be reintroduced at a later stage of production, which helps to maximize the herbs’ flavor and efficacy. To optimize the extraction process, we research the ideal decoction time, temperature, water-to-herb ratio, Pao Zhi method, and maximum concentration ratio of each individual herb.
Once the herbs have been extracted they undergo low temperature vacuum concentration. During this step, the filtered extracts are placed into a concentration pot where the temperature ranges from 40-60° C before the vacuum treatment is applied. Afterwards, the herbs undergo cryoconcentration in an ISO Class 6 clean area that is equipped with more than ten fully-automated production lines. A strict monitoring system put in place for each working procedure ensures the consistency of our products, and only products approved by inspection can enter into the next phase of production.
Our advanced spray drying process instantly dries the extract and ensures that the herbs’ active ingredients are not destroyed, which helps to maintain our herbs’ consistent standards of freshness, color, texture, taste, and water content.
Our spray drying technique uses high-speed centrifugal atomizers to disperse the material into tiny droplets, which are in full contact with hot air to complete constant drying to obtain powder extracts instantly. The temperature of the droplets during drying is relatively low and is especially suitable for drying heat-sensitive materials. It is equipped with a special pneumatic conveying system to separate the extract from the heat and moisture in the system to avoid moisture absorption or agglomeration. Some herbs are ready to be distributed at this stage of production, while others must undergo granulation before they are ready for distribution.
Re-introduction of Essential Oils
During water-based extraction, essential oils are collected from the herbs and preserved to be reintroduced at this stage of production. To maximize the amount of essential oils in the final product, the liquid oils are converted into a solid, before undergoing the Beta-Cyclodextrin procedure. Reintroduction of essential oils increases the herbs’ efficacy while infusing the herbs with their natural aroma.
In the history of Chinese herbal medicine, the development of granulation technology was a key innovation that helped to shape the reform of Chinese herbs. Dry granulation involves mechanically extruding granules. First the dry powder or fine crystalline material is extruded into thin slices, then it is smashed and adjusted into particle size, before being sieved; this process converts the product into uniform particles of a predetermined size. Dry granulation has an advantage over extracts because it can be produced without wetting, mixing, drying, or any other processes.
Laboratories use state-of-the-art technology to examine variables such as quality, concentration ratio, dissolubility, bacterial levels, heavy metals, pesticide residue, and flavacin. The products manufactured by Tianjiang Pharmaceutical meet the standards for both food and drug safety in China and use modern analytical and testing instruments such as CAMAG REPROSTAR, HPLC, GC, and ICP-AES. High-performance liquid chromatography and gas chromatography are also used to determine the level of active ingredients in the granules. Furthermore, thin layer scanning technology is used to identify the fingerprint code of each botanical. Certificates of Analysis provided for every batch include Authentication, Heavy-metal, and Microbiological Analysis.
Once the granule herbs have passed all the quality control inspections, an automated bottling and packaging system is used to finish production. Skilled personnel follow all the Pharmaceutical GMP requirements to finish the final quality check before the products are transferred to the warehouse.
Only packaged products that fulfill the quality control standards are stored and distributed. Finished products are safely stored in a computer-controlled 7000m2 warehouse, in which inventory and distribution are monitored rigorously.